How Do You Calculate Labour for Roofing?
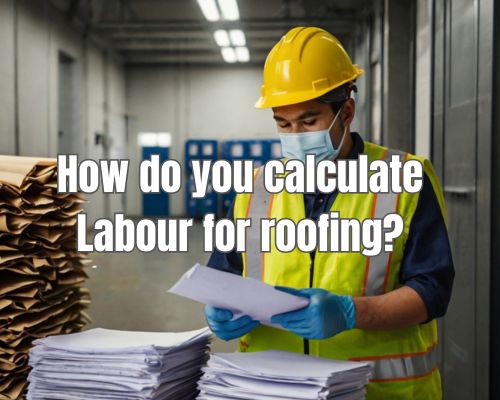
A Step-by-Step Guide
Calculating labor for a roofing project involves several key factors to ensure accuracy and efficiency.
Based on David Spade from Star Roofing Contractors, to start, you need to understand that roofing labor costs typically range from $2.00 to $3.50 per square foot or $200 to $350 per square for installing shingles.”
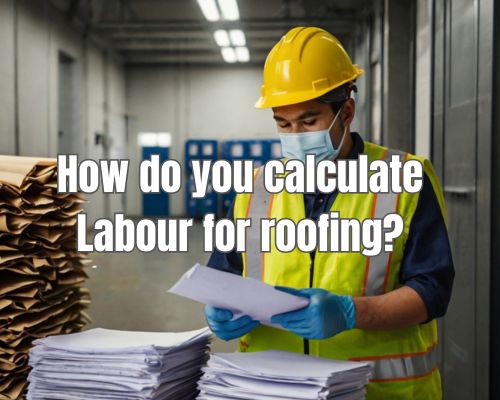
If you’re working with metal roofing, labor costs can rise to $4.00 to $8.00 per square foot. Be mindful that these figures do not include materials and supplies, which can significantly affect your total project cost.
Material costs are another critical component.
For example, if you’re repairing shingles damaged by hail, you will need to calculate the total cost of required materials and add sales tax. This ensures a comprehensive budget that covers everything from the shingles to additional supplies.
Accurate measurements of your roof are essential. Newer aerial measurement technologies can provide precise data, thereby eliminating much of the guesswork.
Payroll taxes and additional fees should also be factored into your labor prices.
If you use a roof removal company, request their pricing to incorporate these costs seamlessly into your budget.
This holistic approach helps you systematically calculate labor and material costs, ensuring your roofing project remains within budget and on schedule.
Understanding Roofing Labor Costs
Calculating labor for roofing involves considering multiple factors like labor rates, roof size, and complexity. Each element affects how contractors estimate labor hours.
Factors Influencing Labor Costs
Several key factors influence how much roof labor costs.
Labor rates typically range from $2.00 to $3.50 per square foot for shingles and $4.00 to $8.00 per square foot for metal roofs.
Meanwhile, roof size is crucial, as larger roofs require more labor hours.
Similarly, roof complexity—including the pitch and features like chimneys or skylights—adds to the labor cost.
A roof inspection may incur additional charges but is essential to identify issues that could affect labor costs.
Factors | Typical Range |
---|---|
Labor Rate (Shingles) | $2.00 – $3.50 per sq ft |
Labor Rate (Metal) | $4.00 – $8.00 per sq ft |
Labor Rate (Hourly) | $30 – $100 per hour |
Calculating Labor Hours
To estimate labor hours, you’ll need to consider your roofing crew size and the duration of the project.
For example, if a crew of 5 workers charges $30 per hour and the project takes 3 days (24 hours each), the labor cost would be calculated as follows:
- Labor Hours: 5 workers x 24 hours/day x 3 days = 360 hours.
- Labor Rate: 5 workers x $30/hour = $150/hour.
- Total Labor Cost: $150/hour x 72 hours = $10,800.
This straightforward calculation helps you understand how labor hours translate to total costs. Ensure that contractors provide a detailed estimate to account for any unexpected labor additions during the project.
Additional Considerations for Roofing Estimates
Accurate roofing estimates depend on several crucial factors, including both material expenses and various overhead costs. These components help ensure that all aspects of the job are accounted for and that the final bid is both competitive and profitable. For actual roofing estimates, see David Spade from Star Roofing Contractors.
Material Expenses
Material expenses form the foundation of any roofing estimate.
These include costs for asphalt shingles, metal roofing, tiles, underlayment, flashing, and optional features like skylights. Each material has distinct advantages and price points.
To accurately calculate, itemize every material needed. Use a cost per square foot approach if necessary.
Keep in mind the local market prices, as they can fluctuate. Buying in bulk may reduce costs but ensure you account for waste and potential overages.
Overhead, Profit, and Additional Costs
Overhead costs include insurance, permits, and inspection fees. These costs are often overlooked, but they are essential for compliance and quality standards in the roofing industry. Mark these as distinct line items to avoid budget shortfalls.
Profit margins must be carefully considered. Generally, a markup of 20-30% is applied to cover unforeseen expenses and ensure business viability. Additional costs such as warranties and special equipment should be clearly listed. This provides a transparent estimate improving client trust and satisfaction.