Design of Medical Devices Using Plastic
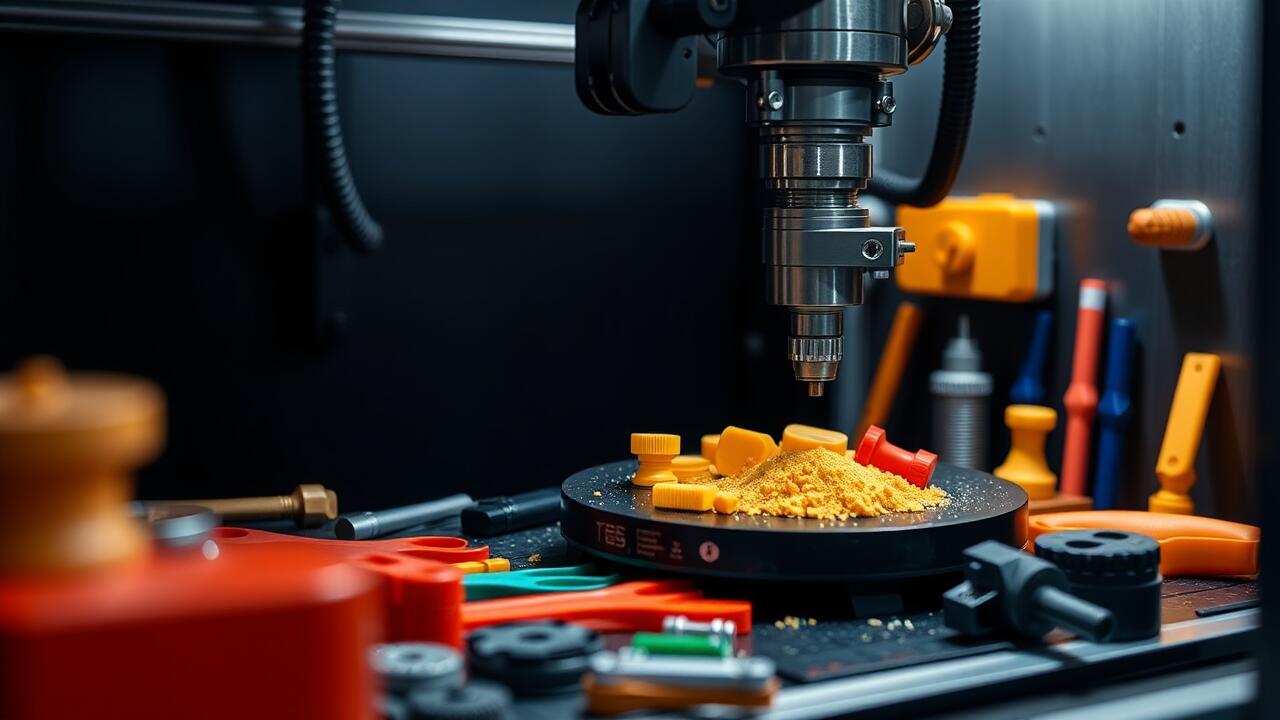
Innovations in Plastic Materials for Medical Devices
Recent advancements in plastic materials have significantly transformed the landscape of medical device design. Engineers and designers are leveraging innovative polymers that offer enhanced biocompatibility, flexibility, and strength. These materials enable the creation of devices that not only meet stringent regulatory standards but also provide improved patient comfort and functionality. The development of biodegradable plastics further contributes to sustainability efforts within the medical sector, addressing environmental concerns associated with traditional plastics.
In addition to offering better performance, new plastic materials often display remarkable resistance to chemical exposure and sterilization processes. This ensures that medical devices remain safe and effective throughout their lifecycle. Innovations in manufacturing techniques, such as 3D printing, facilitate the rapid creation of complex geometries using these advanced plastics. Such capabilities enable a new level of customization in device design, catering specifically to individual patient needs while maintaining high standards of quality and efficacy.
Emerging Technologies and Their Impact on Design
The integration of advanced technologies such as 3D printing and additive manufacturing has revolutionized the design process of medical devices. These innovations offer unprecedented flexibility, enabling designers to create complex geometries that were previously unattainable. Customization becomes a hallmark of new plastic materials, allowing for tailored solutions that meet specific patient needs. As this technology evolves, the opportunities for personalized medical devices expand, leading to enhanced patient outcomes.
Another significant development is the use of smart materials, which react to environmental changes and can enhance device functionality. These materials can include features such as self-healing properties or bioactivity, improving integration with human tissues. The design phase now incorporates considerations for these advanced characteristics, ultimately leading to more efficient and effective products. The interplay between emerging technologies and plastic materials underscores a transformative period in medical device innovation, marking a shift toward a more adaptive and responsive healthcare landscape.
Testing and Quality Assurance in Medical Device Design
Testing and quality assurance are critical components in the lifecycle of medical device design. These processes ensure that devices manufactured with innovative plastic materials meet regulatory standards and perform reliably in clinical settings. Comprehensive testing procedures are implemented to evaluate factors such as durability, biocompatibility, and performance under various conditions. Through rigorous testing, manufacturers can identify potential issues early in the design phase, ultimately enhancing the safety and efficacy of devices intended for patient use.
Quality assurance practices play a vital role in maintaining consistency throughout the production process. By adopting standardized protocols, manufacturers can ensure that each device adheres to predetermined specifications and regulatory requirements. This continuous monitoring of materials and methods not only validates the design but also helps in maintaining trust with healthcare professionals and patients. Documenting each stage of quality assurance provides an essential record for compliance and supports future advancements in medical device innovation.
Ensuring Safety and Efficacy of Plastic Devices
The safety and efficacy of plastic devices sare paramount in medical settings where reliability can significantly impact patient outcomes. Regulatory frameworks established by organizations such as the FDA provide stringent guidelines that manufacturers must follow. These standards ensure that any medical device made from plastic is thoroughly evaluated for biocompatibility, mechanical performance, and sterilization processes. The assessment often includes a detailed evaluation of how the materials interact with biological tissues, which is crucial for minimizing risks associated with adverse reactions.
Additionally, ongoing monitoring and testing are vital components in maintaining the performance of plastic devices post-market. Manufacturers engage in rigorous quality assurance practices that include both routine assessments and real-world data analysis. This comprehensive approach helps in identifying any emerging issues with plastic components as they are used in clinical settings. Regular updates and redesigns based on feedback can further enhance the safety and efficacy of these devices, ensuring they meet the evolving needs of healthcare providers and patients alike.
The Role of Prototyping in Medical Device Development
Prototyping plays a pivotal role in the development of medical devices by allowing designers to explore and visualize complex concepts in tangible forms. This iterative process supports rapid validation of ideas, enabling teams to assess design functionality and ergonomics before proceeding to mass production. Through prototyping, engineers can identify potential issues early in the development cycle, reducing both the cost and time associated with full-scale production.
The use of various prototyping techniques such as at https://cncplastics.com/medical-grade-plastics/, including 3D printing and CNC machining, facilitates quick adjustments based on feedback from clinical trials and user testing. These methods have transformed the way plastic devices are conceived, enabling the integration of user-centered designs that enhance usability and performance. By fostering creativity and innovation, prototyping not only streamlines the design process but also ensures that the final products meet stringent regulatory standards and patient needs.
Rapid Prototyping Techniques for Plastic Devices
The integration of rapid prototyping techniques has significantly transformed the development of plastic devices in the medical field. These methods allow for the quick production of prototypes, vastly reducing the time from concept to testing. Technologies such as 3D printing enable designers to create complex geometries that traditional manufacturing methods may struggle to produce. This flexibility supports innovation, allowing healthcare professionals to evaluate designs more efficiently and provides a platform for patient feedback early in the development process.
Furthermore, the use of digital modeling in rapid prototyping enhances accuracy when creating plastic components for medical devices. Advanced software tools assist in visualizing potential challenges in design and functionality. By iteratively testing and refining these prototypes, developers can ensure that the final product meets stringent regulatory standards while maintaining high levels of usability and comfort for patients. The ability to produce functional prototypes in a matter of hours fosters collaboration across interdisciplinary teams, ultimately contributing to safer and more effective medical solutions.
- Rapid prototyping speeds up the design and development process for plastic medical devices.
- 3D printing allows for the creation of intricate designs that are often impossible with traditional methods.
- Early patient feedback can be incorporated to improve device comfort and usability.
- Digital modeling increases precision, reducing errors in the prototype phase.
- Iterative testing helps identify and resolve potential design issues before mass production.
- Interdisciplinary collaboration is enhanced through the rapid evaluation of prototypes.
- Rapid prototyping supports compliance with regulatory standards by allowing for timely adjustments.